Студентам > Рефераты > История развития электроники
История развития электроникиСтраница: 4/5
4.5.2
Первыми транзисторами выпущенными отечественной
промышленностью были точечные транзисторы, которые предназначались для усиления
и генерирования колебаний частотой до 5 МГц. В процессе производства первых в
мире транзисторов были отработаны отдельные технологические процессы и
разработаны методы контроля параметров. Накопленный опыт позволил перейти к
выпуску более совершенных приборов, которые уже могли работать на частотах до
10 МГц. В дальнейшем на смену точечным транзисторам пришли плоскостные,
обладающие более высокими электрическими и эксплуатационными качествами. Первые
транзисторы типа П1 и П2 предназначались для усиления и генерирования
электрических колебаний с частотой до 100 кГц. Затем появились более мощные
низкочастотные транзисторы П3 и П4 применение которых в 2-х тактных усилителях
позволяло получить выходную мощность до нескольких десятков ватт. По мере
развития полупроводниковой промышленности происходило освоение новых типов
транзисторов, в том числе П5 и П6, которые по сравнению со своими предшественниками
обладали улучшенными характеристиками. Шло время, осваивались новые методы
изготовления транзисторов, и транзисторы П1 – П6 уже не удовлетворяли
действующим требованиям и были сняты с производства. Вместо них появились
транзисторы типа П13 – П16, П201 – П203, которые тоже относились к
низкочастотным непревышающим 100 кГц. Столь низкий частотный предел объясняется
способом изготовления этих транзисторов, осуществляемым методом сплавления.
Поэтому транзисторы П1 – П6, П13 – П16, П201 – П203 называют сплавными.
Транзисторы способные генерировать и усиливать электрические колебания с
частотой в десятки и сотни МГц появились значительно позже – это были
транзисторы типа П401 – П403, которые положили начало применению нового
диффузионного метода изготовления полупроводниковых приборов. Такие транзисторы
называют диффузионными. Дальнейшее развитие шло по пути совершенствования как
сплавных, так и диффузионных транзисторов, а так же созданию и освоению новых
методов их изготовления.
5. Предпосылки появления
микроэлектроники
5.1 Требования
миниатюризации электрорадиоэлементов со стороны разработчиков радиоаппаратуры.
С появлением биполярных полевых транзисторов начали
воплощаться идеи разработки малогабаритных ЭВМ. На их основе стали создавать
бортовые электронные системы для авиационной и космической техники. Так как эти
устройства содержали тысячи отдельных ЭРЭ(электрорадиоэлементов) и постоянно
требовалось все большее и большее их увеличение, появились и технические
трудности. С увеличением числа элементов электронных систем практически не
удавалось обеспечить их работоспособность сразу же после сборки, и обеспечить,
в дальнейшем, надежность функционирования систем. Даже опытные сборщики и
наладчики ЭВМ допускали несколько ошибок на 1000 спаек. Разработчики
предполагали новые перспективные схемы, а изготовители не могли запустить эти
схемы сразу после сборки т.к. при монтаже не удавалось избежать ошибок, обрывов
в цепи за счет не пропаев, и коротких замыканий. Требовалась длинная и
кропотливая наладка. Проблема качества монтажно-сборочных работ стало основной
проблемой изготовителей при обеспечении работоспособности и надежности
радиоэлектронных устройств. Решение проблемы межсоединений и явилось
предпосылкой к появлению микроэлектроники. Прообразом будущих микросхем
послужила печатная плата, в которой все одиночные проводники объединены в
единое целое и изготавливаются одновременно групповым методом путем
стравливания медной фольги с плоскостью фольгированного диэлектрика.
Единственным видом интеграции в этом случае являются проводники. Применение
печатных плат хотя и не решает проблемы миниатюризации, однако решает проблему
повышения надежности межсоединений. Технология изготовления печатных плат не
дает возможности изготовить одновременно другие пассивные элементы кроме
проводников. Именно поэтому печатные платы не превратились в интегральные
микросхемы в современном понимании. Первыми были разработаны в конце 40-х годов
толстопленочные гибридные схемы, в основу их изготовления была положена уже
отработанная технология изготовления керамических конденсаторов, использующая
метод нанесения на керамическую подложку через трафареты паст, содержащих
порошок серебра и стекла. Переход к изготовлению на одной подложке нескольких
соединенных между собой конденсаторов, а затем соединение их с композиционными
резисторами, наносимыми также с помощью трафарета, с последующим вжиганием
привело к созданию гибридных схем, состоящих из конденсаторов и резисторов.
Вскоре в состав гибридных схем были включены и дискретные активные и пассивные
компоненты: навесные конденсаторы, диоды и транзисторы. В дальнейшем развитии
гибридных схем навесным монтажем были включены сверхминиатюрные
электровакуумные лампы. Такие схемы получили название толстопленочные гибридные
интегральные микросхемы (ГИС). Тонкопленочная технология производства интегральных
микросхем включает в себя нанесение в вакууме на гладкую поверхность
диэлектрических подложек тонких пленок различных материалов(проводящих, диэлектрических,
резистивных).
В 60-е годы огромные усилия исследователей были
направлены на создание тонкопленочных активных элементов. Однако надежно
работающих транзисторов с воспроизводимыми характеристиками никак не удавалось
получить, поэтому в тонкопленочных ГИС продолжают использовать активные
навесные элементы. К моменту изобретения интегральных микросхем из полупроводниковых
материалов уже научились изготавливать дискретные транзисторы и резисторы. Для
изготовления конденсатора уже использовали емкость обратно смещенного
p-n
перехода. Для изготовления резисторов использовались омические свойства кристалла
полупроводника. На очереди стояла задача объединить все эти элементы в одном
устройстве.
5.2 Основы развития
технологии микроэлектроники.
5.2.1
Развитие микроэлектроники определяется уровнем
достигнутой микротехнологии.
Планарная технология. При планарной технологии
требуется обеспечить возможность создания рисунка тонких слоев из материала с
различными электрическими характеристиками, чтобы получить электронную схему.
Важная особенность планарной технологии заключается в ее групповом характере: все
интегральные схемы (ИС) на пластине изготавливают в одном технологическом
цикле, что позволяет одновременно получать несколько полупроводниковых схем.
5.2.1.1
Технологические процессы получения тонких пленок.
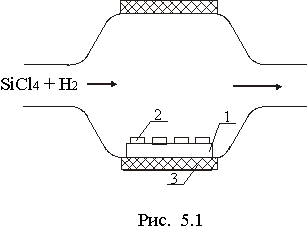
1) Эпитаксия (упорядочение) – процесс
наращивания на кристаллической подложке атомов упорядоченных в
монокристаллическую структуру. с тем чтобы структура наращиваемой пленки
полностью повторила кристаллическую ориентацию подложки. Основное достоинство
техники эпитаксии состоит в возможности получения чрезвычайно чистых пленок при
сохранении возможности регулирования уровня легирования. Применяют три типа
эпитаксиального наращивания: газовую, жидкостную и молекулярную.
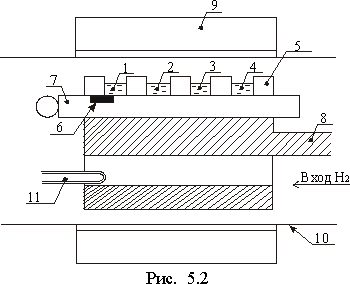
При газовой эпитаксии водород с примесью
четырех хлористого кремния (SiCl4 + H2) с контролируемой концентрацией пропускают через
реактор (Рис. 5.1), в котором на графитовом основании (1) расположены
кремниевые пластины (2). С помощью индукционного нагревателя графит
прогревается выше 1000 0С эта температура необходима для обеспечения
правильной ориентации осаждаемых атомов в решетке и получении
монокристаллической пленки. В основе процесса лежит обратимая реакция:
SiCl4 + 2H2 ↔ Si + 4HCl – прямая
реакция соответствует получению эпитаксиальной пленки, обратная реакция
травлению подложки. Для легирования эпитаксиальной пленки в газовый поток
добавляют примесные атомы. Фосфорит (PH3) используют в качестве донорной примеси, а диборан (B2 H3) в качестве
акцепторной примеси.
При жидкостной эпитаксии получают многочисленные
структуры из разных материалов. На Рис. 5.2: 1, 2, 3, 4 – растворы
5 – скользящий графитовый держатель
растворов
6 – подложка
7 – основной графитовый держатель
8 – толкатель
9 – электрическая печь
10 – кварцевая труба
11 – термофара
Подвижная конструкция с различными растворами
последовательно подводит растворы к подложке. Таким образом получают
гетеропереходы с различными материалами толщиной менее 1 мкм (Ge –
Si, GaAs
– GaP)
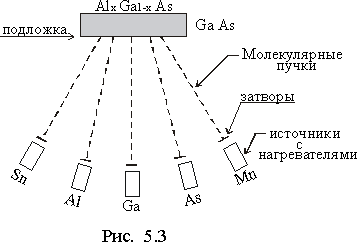
Молекулярно-лучевая эпитаксия проводится в
сверхвысоком вакууме и основана на взаимодействии нескольких молекулярных
пучков с нагретой монокристаллической подложкой. На Рис. 5.3 иллюстрируется
процесс получения соединения AlxGa1–xAs. Каждый нагреватель содержит тигель, являющимся
источником молекулярного пучка одного из основных элементов пленки. Температура
каждого нагревателя выбирается таким образом, чтобы давление паров, испаренных
материалов, было достаточно для образования молекулярных пучков. Подбором
температуры нагревателя и подложки получают пленки со сложным химическим
составом. Дополнительное управление процессом выращивания осуществляется с
помощью специальных заслонок, расположенных между нагревателем и подложкой.
Метод молекулярно-лучевой эпитаксии наиболее перспективен для твердотельной
электроники в которой существенную роль играют слоистые структуры субмикронных
размеров.
2) Окисление. Слой двуокиси кремния формируется
обычно на подложке за счет химического соединения атомов кремния с кислородом,
который подается к поверхности кремниевой подложки нагретой технической печи до
температуры 900-1200 оС.
Рис. 5.4 : 1 – подложка
2 – кварцевая лодочка
3 – нагреватель
4 – кварцевая труба
Окислительной средой может быть сухой или влажный
кислород. Окисление происходит быстрее в атмосфере влажного кислорода, поэтому
оно используется для получения толстых пленок SiO2. Наиболее часто используется толщина окисла
составляющая десятые доли мкм, а верхний практический предел 1–2 мкм.
5.2.2
Литографические процессы используемые для формирования токологии микросхем.
5.2.2.1 Фотолитография.
Фотолитография является основным технологическим
процессом в микроэлектронике при получении линий шириной до 1 мкм и его долей.
Сначала изготавливают оригинал топологии микросхемы в сильноувеличенном размере
(до 500 раз). Затем делают фотографию с уменьшением в 100 раз, затем в 10 раз и
т.д. пока окончательное изображение на пластине не будет точно соответствовать
требуемой схеме. Полученная фотопластина используется в качестве маски для
передачи рисунка на поверхность подложки. Рассмотрим фотолитографический
процесс для получения отверстия в слое двуокиси кремния расположенном на
подложке. Рис. 5.5
1 – стеклянный фотошаблон
2 – фоторезист
3 – SiO2 (окись
кремния)
4 – кремниевая подложка
5 – светонепроницаемый рисунок на фотоэмульсии
6 – ультрафиолетовое излучение
Этапы:
а) Первичное покрытие
б) Контактная печать
в) После проявления
г) После травления
д) После удаления фоторезиста
Сначала на окисный слой наносят фоторезист (2), затем
к фоторезисту прикладывают стеклянный фотошаблон (1) с рисунком соответствующим
той части окисла, которая должна быть удалена (5). Экспонируют фотошаблон в
ультрафиолетовых лучах (6). Проявляют. В процессе проявления не экспонированные
участки фоторезиста (2) растворяются. Окисный слой в окне стравливают кислотным
раствором и удаляют оставшийся слой фоторезиста – такой метод называется
методом контактной печати. Кроме того используют проекционную печать, когда
между фотошаблоном и подложкой располагают оптические линзы.
5.2.2.2
Электронно-лучевая литография.
Для получения рисунка методом электронной литографии
применяют два способа:
1) Электронный луч, управляемый ЭВМ,
перемещается заданным образом по поверхности подложки.
2) Электронный пучок проходит через
специальные маски.
В первом случае применяют два типа сканирующих систем
– растровую и векторную. В растровой системе электронный луч модулируется по
интенсивности и построчно проходит по всей поверхности подложки. В векторной
системе электронный луч отклоняется таким образом, что его след на резисте
точно соответствует необходимому рисунку.
Во втором варианте фотокатод располагают на
поверхности оптической маски с заданным рисунком. Ультрафиолетовые лучи
облучают фотокатод сквозь маску, что приводит к эмиссии электронов с фотокатода
в соответствующих рисунку областях. Эти электроны проецируются на поверхность
резиста с помощью однородных совпадающих по направлению электростатических и
магнитных полей. Разрешающая способность такой системы соответствует субмикронным
размерам по всей площади подложки.
5.2.2.3 Рентгеновская
литография.
Метод рентгеновской литографии иллюстрируется на Рис.
5.6 :
1а – электронный луч
2а – мишень
3а – рентгеновские лучи
1 – прозрачный материал
2 – поглотитель
3 – прокладка
4 – полимерная пленка (резист)
5 – подложка
Маска состоит из мембраны (4) прозрачной для
рентгеновских лучей, поддерживающей пленку, которая имеет заданный рисунок и
сделана из материала сильно поглощающего рентгеновские лучи. Эта маска
располагается на подложке покрытой радиационно чувствительным резистом. На
расстоянии Д от маски находится точечный источник рентгеновского излучения,
которое возникает при взаимодействии сфокусированного электронного луча с
мишенью. Рентгеновские лучи облучают маску, создавая проекционные тени от
поглотителя рентгеновских лучей на полимерные пленки. После экспонирования
удаляют либо облученные области при позитивном резисте, либо не облученные при
негативном резисте. При этом на поверхности резиста создается рельеф,
соответствующий рисунку. После получения рельефа на резисте подложка
обрабатывается травлением, наращиванием дополнительных материалов,
легированием, нанесением материала через окна в рисунке резиста.
5.2.2.4 Ионно-лучевая
литография.
|